Rigid-Flex PCB
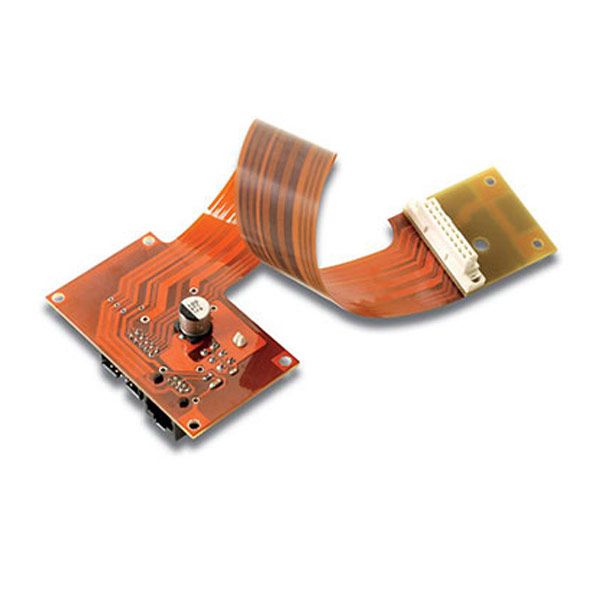
What is rigid-flex PCB?
A rigid-flex PCB is a board that is made up of flexible PCB and rigid PCB, and rigid-flex PCB has multiple layers of both flexible and rigid technologies so that it could be able to do better at an optimum level without the risk of breaking. A rigid-flex PCB can be completely custom to meet the demands of application for a variety of vias that are used, materials and track widths.
As you know, the rigid-flex PCB does not be in a fragile state, on the contrary, rigid-flex PCB is in a steady state of a curve. The shape of rigid-flex PCB takes as a spring, which it will go back to its original state if you stretch or compress.
Benefits of Rigid-Flex PCB
An reliable interconnection;
Reduce the costs of logistical and assembly;
A rigid part for mounting the components, a flexible part for the movement;
It’s very reliable and space-saving because of Connections without connectors;
Make it easy to do assembly because of flexibility and lack of connectors connections;
There will not any incorrect assembly owing to the integrated interconnection, which can prevent incorrect assembly during maintenance work;
There will have many options for impedance controlled tracks; it can realize impedance control in both the rigid and the flex parts.
Rigid-flex PCB applications
The rigid-flex PCB has a variety of applications in different kinds of accessories and equipment that are used on a daily basis. One of the most obvious uses is the application of smartphone. In the present, it needs to be incredibly thin but highly functional for the smartphones, and only the rigid-flex technology can it achieve.
Another famous application of rigid-flex PCB is various computer electronics equipment. The hard drive, one of the many components with rigid-flex technology. It can catch up with the ever-increasing write speeds of today’s computer. It’s great for a hard drive to use a rigid-flex PCB, because it can make the hard drive cool down.
In consumer products, rigid-flex PCB doesn't just maximize space and weight but greatly improves reliability, eliminating many needs for solder joints and delicate, fragile wiring that are prone to connection issues. However, rigid-flex PCB can nearly be used to benefit all advanced electrical applications including testing equipment, tools and automobiles.
Why rigid-flex PCB?
Rigid-flex PCBs are a way to remove the electronic design, connectors, flexible cables as well as discrete wiring. Comparing to other boards, it has great electrical performance as the circuits are integral to the overall construction. All of the electrical and mechanical connections are internally contained within the rigid-flex PCB so that it can provide much improved service reliability and electrical performance for electronics designer.
The reasons why rigid-flex PCB is better than rigid PCB and flexible PCB is that it has the advantage of the reliability, weight reduction, strength and space-saving, while rigid-flex PCB gets to a higher cost. What’s more, rigid-flex PCBs provide the best advantages of rigid and flex PCBs in one solution. There is the applications of rigid flex PCB as allows:
High-density applications. Sometimes it’s hard to accept all of the cables and connectors that an electronic PCB design would be necessary within a small enclosure. Needless to say, rigid-flex PCB can fold into the tiny profiles, so it can save more spaces in these cases.
High-reliability applications. It’s possible for the connectors with flexible cables to fail if an assembly will be exposed to excessive or repeated shock, or high vibration environments. Rigid-flex PCB has a great reliability even when subjected to shock applications and extreme vibration.
Five or more rigid PCBs. An integrated rigid flex solution is often the optimal and most cost-effective choice if your application will ultimately involve five or more rigid boards connected to one another with flex cables.